The symptoms
The vehicle was a 2004 Seat Arosa 1.4 TDI (3-cylinder) that had found its way to a specialist diesel shop with a no-start complaint. The car began by occasionally cutting out, but progressively got worse and eventually turned into a complete no-start. It would crank fine but just wouldn’t fire. Checking the system with the scan tool, I found no DTCs logged. Ordinarily I’d suspect that the codes had already been erased at some point down the line, but after several cranks I couldn’t get any DTCs myself.
Looking for the fault
Let us start at the beginning by monitoring cause and effect. Here, CKP and CMP are monitored along with the output stage to the injectors.
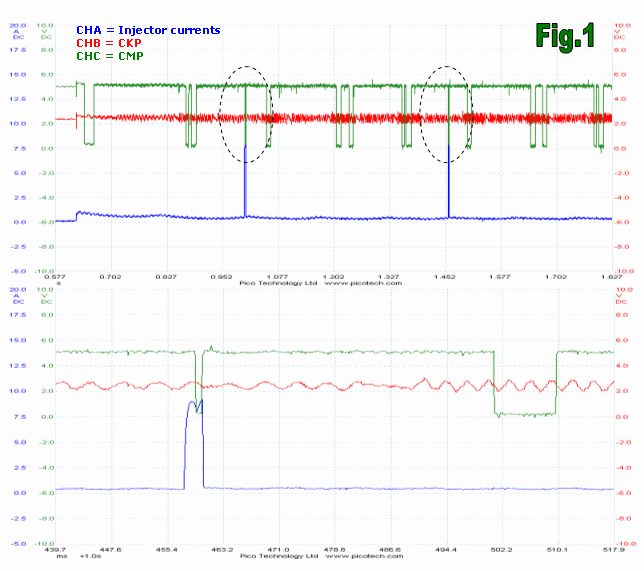
Fig.1 shows a typical recording taken during cranking. There are a few anomalies, one being the presence of a CMP signal drop during an injector period that is released when the injector is released. This cam clearly had three unique groups of identifiers each relating to a particular cylinder, so why the need for a fourth CMP pulse? Analysing the other cam identifiers, they were all fairly short in duration, with the shortest measuring 4.5 ms at cranking speed. Our suspect signal drop was measuring significantly less at 0.7 ms, so it’s either a very narrow cam tooth or is in fact a problem. I’m leaning towards the latter. There was something else which didn’t make sense: on this system all injectors share a power cable from the ECM, and my current clamp was monitoring this cable to get an overview of all injectors. According to the capture only one injector command is present.
A short time into the investigation I had a change of fortune when the engine started. Scrolling back through the recorded captures, I found Fig. 2.
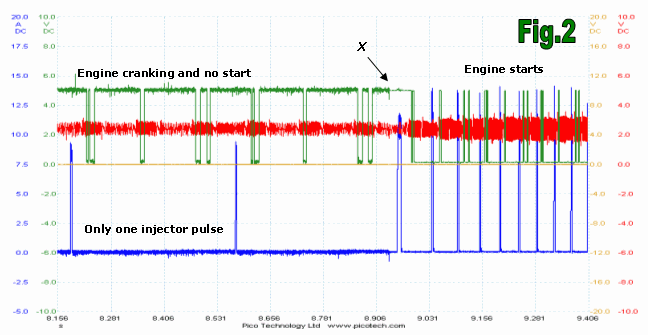
The significant difference now, with the engine running, was in the CMP sensor: note the signal biasing that has changed from 5 V to 0 V. Even though the CMP had been delivering the cam identifiers, it was the sequence of high and low logic states that had been incorrect. There are possible mechanical influences to be aware of when you see a flawed CKP or CMP signal, but this was not a mechanical problem. A faulty CMP sensor? Possibly, but it doesn’t explain our injector in Fig.1 interfering with the CMP signal. And what about the sudden change in signal stability at point X? It seems an odd coincidence that immediately after this X the whole start-up operation changed.
Power to the CMP sensor
By now there are more questions than answers, and when this happens I pick one diagnostic trail and stick to it. With each piece of the puzzle so far involving the CMP sensor at some level, the next methodical check is to see if it was being powered up correctly. Always the basics first.
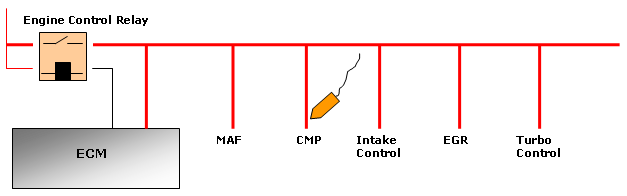
On this model the CMP receives full battery voltage from an engine control relay. This power supply is shared amongst other sensors and actuators, including the ECM which in turn powers the injector circuits.
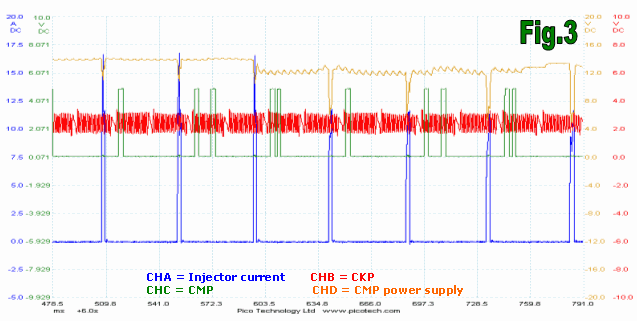
Fig.3 was taken with the engine at idle and just beginning to stumble. We have a problem! The power supply feeding the CMP sensor is suffering under electrical load and it’s evident that the injectors are having the greatest impact, so there is more to this problem than just the CMP sensor. Even though the CMP signal isn’t being affected here (yet) it’s easy to predict that the problem will get much worse during cranking, and this could offer an explanation of Fig.1: the CMP sensor simply gave in. There is a perfect relationship displayed here between voltage and current. We can see that, as the voltage supply deteriorates, so does the current available to drive the component, but it’s the high current demand that is making the poor voltage supply evident. Cause and effect, then back to cause again. I picked out the lowest supply voltage at a shocking 4.3 V, but delivering a surprising 11 A – being helped by the boost capacitor in this HDI system. Even without the idle stumble, it is still clear that the same problem exists in the preceding injector events, where the injector current is a healthy 17 A while the voltage supply drops sharply to 11 V.
The root fault is undoubtedly a high-resistance power source. I found that all components connected to the power supply were suffering to the same extent, so the next logical step was to look at the control relay itself.
The relay was found in different stages of solder joint fatigue. Its contacts weren’t brilliant either, which I have to say is surprising on a 4-year-old car with 21,000 miles on the clock. The bad relay had introduced a high resistance in the current path to several engine components, creating a basic voltage divider circuit.
The engine control relay on VAG drive systems is a recurring nuisance and can exhibit all kinds of symptoms. This unwanted high resistance was having unpredictable effects on the circuit, demonstrating that not all relay problems are simple “not working” conditions.
Get a new relay.
After the repair
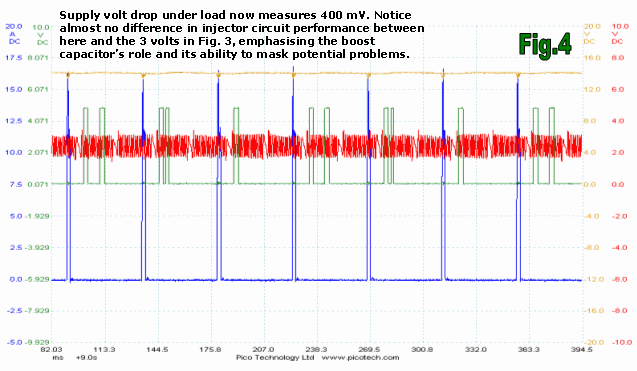
The new relay was now delivering full battery voltage, reducing cranking duration and improving running conditions in general.
I returned to a few early observations to see if this poor relay problem could answer some questions. I’ve already covered the CMP sensor drop-out in Fig.1 and can only conclude that the low supply voltage available during cranking worsened the problem, and the sensor just gave up as the injector circuit consumed all available current. Incidentally, even the boost capacitor circuit could only manage an injector current of 7.5 A. The mystery X in Fig.2 was most likely electrical noise from the unstable power supply. In particular, the fractured PCB joint showed surface scorches as evidence of arcing.
Finally this no-start problem had no codes logged. I saw my first code – INJECTOR CIRCUIT THRESHOLD – after the engine started and only during the rough idle period. Yet, during repeat cranking with a poor system voltage, reduced signal ranges, and incorrect actuator outputs, I saw NO DTCS LOGGED. You may want to re-evaluate how much your fault-finding strategy relies on trouble codes.
其它輔導(dǎo)資料 >
|